ABSOLUTE PRESSURE
This is the pressure measured from absolute zero (vacuum).
We calculate absolute pressure by adding atmospheric pressure to
gauge pressure. At sea level, gauge pressure is 0 psi.
Absolute pressure is 14.7 psi.
In the metric system, atmospheric pressure is usually stated as
one "bar or one atmosphere." |
------------------------------------------------------------------------------------------------------------------------ |
Actuator |
Device used to open/close or control the valve. Key
types include electrical, hydraulic and pneumatic. Movement may be
quarter-turn or multi-turn. Actuators may be used when (i) valves
are remotely located (eg, on pipelines) (ii) valves are located in
hazardous areas (iii) manual operation would be time-consuming
(eg, with larger valves)
------------------------------------------------------------------------------------------------------------------------ |
ATMOSPHERIC PRESSURE
At sea level, atmospheric pressure is 14.7 psi. or in the
metric system, 1 bar of pressure. The atmospheric pressure changes
with altitude and weather conditions.
------------------------------------------------------------------------------------------------------------------------ |
Air valve |
Valve that is used to control the flow of air. Flows
are normally small, so solenoid valves are suited.
------------------------------------------------------------------------------------------------------------------------ |
Bases
are compounds that ionize (or break down) to
form a hydroxide
ion (OH-) ions in water. Substances with Ph
values of seven or higher are considered to be bases.
Litmus paper turns blue when exposed to a base.
In the math and science world, a base is a multiplier in
a numbering system. In a decimal
system, each digit position is worth 10x the position to its right.
In binary,
each digit position is worth 2x the position to its right
------------------------------------------------------------------------------------------------------------------------ |
Back pressure |
The pressure exerted on the downstream side of a
valve seat.
------------------------------------------------------------------------------------------------------------------------ |
Ball valve |
A quarter-turn valve with a spherical closing
element held between two seats. Characteristics include quick
opening and good shut-off. Ball valves are widely used as on/off
valves in the chemical process and other industries. Special
designs (with V notches or fingers) are available for throttling
applications. Larger valves with heavier balls (eg, on pipelines)
may use trunnions to help support the ball and prevent damage to
soft internals. Designs are typically, one, two or three piece.
------------------------------------------------------------------------------------------------------------------------ |
Bellows |
Sealing device which prevents line media leaking
between the stem and the body.
------------------------------------------------------------------------------------------------------------------------ |
Butterfly valve |
A quarter-turn valve which has a circular disk as
its closing element. The standard design has the valve stem
running through the disk, giving a symmetrical appearance. Later
designs off-set the stem, so that the disk ‘cams’ into the
valve seat. Advantages include less wear and tear on the disk and
seats, and tighter shut-off capabilities. Many design types are
available including inexpensive Teflon or resilient seats for use
in water (treatment) plants, etc. More expensive metal seats can
be used where high temperatures or aggressive chemicals are
encountered. So-called “High Performance” butterfly valves
offer zero leakage designs and have been applied in both the
chemicals and hydrocarbon processing sectors.
------------------------------------------------------------------------------------------------------------------------ |
Bypass valve |
A small bore valve fitted in parallel to a larger
main valve. Bypass valves are used to reduce the differential
pressure across the main valve before this latter valve is opened
(as otherwise this larger, more expensive valve, may suffer damage
to internal components).
------------------------------------------------------------------------------------------------------------------------ |
|
|
Check valve |
A valve that is designed to allow the fluid to flow
in a given direction but closes to prevent backflow. Types include
swing check, tilting disc check and wafer check. Check valves (also
called non-return valves) are usually self-acting.
------------------------------------------------------------------------------------------------------------------------ |
Control valve |
A valve which regulates the flow or pressure of a
fluid. Control valves normally respond to signals generated by
independent devices such as flow meters, temperature gauges, etc.
Control valves are normally fitted with actuators and positioners.
Pneumatically-actuated globe valves are widely used for control
purposes in many industries, although quarter-turn types such as (modified)
ball and butterfly valves may also be used.
------------------------------------------------------------------------------------------------------------------------ |
Cryogenic valves |
These are valves suited for use at temperatures
below - 40 degrees Celsius.
------------------------------------------------------------------------------------------------------------------------ |
Diaphragm valve |
A bi-directional valve which is operated by applying
an external force to a flexible element, or diaphragm (typically
an elastomer). Diaphragm valves may be used for slurries (where
other valve designs might clog) or in hygienic applications.
Diaphragm valves constitute the third major type of linear movement
valves. The stem of the valve is used to push down a flexible
diaphragm, which in turn blocks the path of the fluid. There are two
different classifications of diaphragm valve based on the geometry of
the valve body:
 |
Weir type - A weir is cast into the body, and when
closed, the diaphragm rests on the weir, restricting the flow (see
Figure (a) below ).
 |
Straight-through type - The bore runs laterally through
the body and a wedge shaped diaphragm is used to make the closure
(see Figure (b) below).
|
|
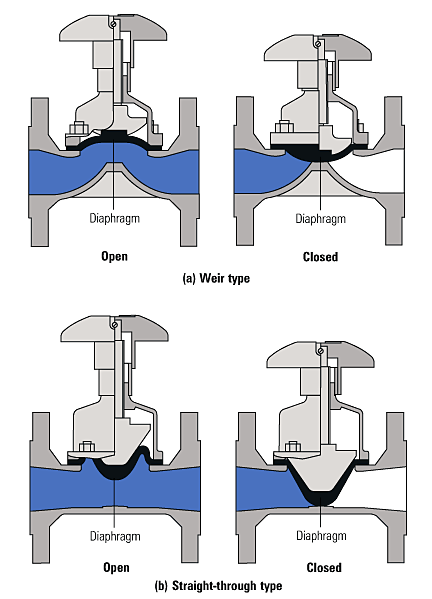 |
The weir type (a) and
straight-through type (b) diaphragm valves
|
The main advantage of a diaphragm valve is the fact
that the diaphragm isolates the moving parts of the valve from the
process fluid. They are therefore suitable for handling aggressive
fluids and for those containing suspended solids. In addition, as the
bonnet assembly is not exposed to the fluid, it can be made from
inexpensive materials such as cast iron, thereby reducing the overall
cost. The development of new diaphragm materials enables diaphragms to
be used on most fluids. Their application is however limited by the
temperature that the diaphragm can withstand - typically less than 175°C.
Diaphragm valves are generally used on process fluid applications.
------------------------------------------------------------------------------------------------------------------------
|
Diverter valve |
A valve which can change the direction of the flow
of a medium to two or more different directions.
------------------------------------------------------------------------------------------------------------------------ |
Double block and bleed |
A valve configuration in which positive shut-off is
achieved at both the inlet and outlet sides. A small port is
fitted to discharge fluid in the intermediate space. Fitting a gas
detector to the port provides assurance of the integrity of the
upstream seal. This configuration is often required to isolate
high pressure sections of a system to facilitate safe maintenance,
etc.
------------------------------------------------------------------------------------------------------------------------ |
Electric actuators |
Actuator which uses an electric motor to operate the
valve stem.
------------------------------------------------------------------------------------------------------------------------ |
Extended bonnet |
Used when the media is at high or low temperatures,
to avoid damage to the sealing elements.
------------------------------------------------------------------------------------------------------------------------ |
Float valve |
A valve which automatically opens or closes as the
level of a liquid changes. The valve is operated mechanically by a
float which rests on the top of the liquid.
------------------------------------------------------------------------------------------------------------------------ |
Full bore |
Term used e.g. of a ball valve, to indicate that the
internal diameter of the valve opening is the same as that of the
piping to which it is fitted.
------------------------------------------------------------------------------------------------------------------------ |
Gate valve |
A multi-turn valve which has a gate-like disk and
two seats to close the valve. The gate moves linearly,
perpendicular to the direction of flow. This type of valve is
normally used in the fully opened or fully closed position; it is
not suited to throttling applications. Gate valves provide robust
sealing, and are used extensively in the petrochemicals industries.
This class of valves also includes knife gate valves, conduit gate
valves and wedge gate valves. Knife gate valves have much thinner
gates with a knife-like edge, making them suited to use with
floating solids, eg, as in the pulp & paper industries.
Conduit gate valves have a rectangular disk as the closing
element. One half of the disk is solid, to close the valve, the
other has a circular port, which can be used to open the valve.
Wedge gate valves have a wedge-shaped gate which ‘wedges’
between floating seats to close the valve tightly.
Gate valves are probably the most common valves in use today due to
their widespread use in domestic water systems, but it should be noted
that their popularity in industry has declined in recent years.
However, they are still used where an uninterrupted flow is required,
because the gate fully retracts into the bonnet, creating a minimal
pressure drop, when the valve is in an open position. Gate valves are
specifically intended for use in isolation applications.
A gate valve consists of four main components, the body, bonnet (or
cover), gate and stem. A typical gate valve is shown in Figure below.
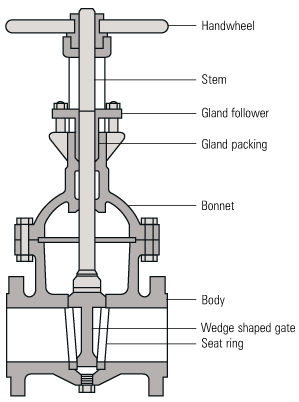 |
Typical wedge gate valve
|
The gate, which slides between the seats, is lifted in
a direction at right angles to the flow until clear of the flow path.
The fact that the gate fully retracts into the bonnet ensures that the
pressure drop across the valve is low.
Gate valves are divided into a number of different classes, depending
on the design of the gate and its seating faces.
Solid wedge gate valve
The gate is wedge shaped and it seats on corresponding faces in the
valve body. The mechanical advantage of the activating thread,
together with the wedge angle, enables adequate seating forces to be
applied against the fluid pressure without excessive handwheel effort.
The seat can sometimes be coated with PTFE to assist a high integrity
shut-off. A typical solid wedge gate valve is shown in Figure 12.1.1.
Flexible wedge gate valve
Although there are several types of flexible wedge gate valves, they
all make use of a flexible two-part disc, which is shaped like two
wheels on a very short axle. The flexibility of the disc ensures tight
seating over a wide range of temperatures and pressures.
The most common type of flexible wedge gate valve used in steam
applications is the parallel slide valve. The two plates that
constitute the gate are held against the seat by a spring, encased
between them. The fluid pressure moves the upstream disc off its seat,
and the force is transferred onto the downstream disc, thereby
ensuring a tight shut-off. The high degree of flexibility in the gate
allows for expansion and contraction when subjected to temperature
variations, making it suitable for use in steam systems.
------------------------------------------------------------------------------------------------------------------------
|
Gearboxes |
Used to ensure easier operation of larger valves,
particularly ball valves.
------------------------------------------------------------------------------------------------------------------------ |
Globe valve |
A multi-turn valve with a closing element that moves
perpendicularly to the valve body seat and generally seals in a
plane parallel to the direction of flow. This type of valves is
suited both to throttling and general flow control.
Globe valves constitute a major class of linear movement valves; they
have become more popular than gate valves as there is a wide variety
of configurations available to suit most applications. The movement of
fluid through the valve seat is longitudinal to the operating motion
of the obturator; this means that for a valve in which the inlet and
outlet are horizontally opposed, the fluid must follow a changing
course. The main advantage of this arrangement is that a globe valve
opens more rapidly than a gate valve as the disc only needs to move a
small distance from its seat to allow full flow. This is an advantage
when there is frequent operation of the valve. The disadvantage is
that the fluid has to change course, increasing the resistance to flow
and generating turbulence. This results in a higher pressure drop
across a globe valve than a gate valve.
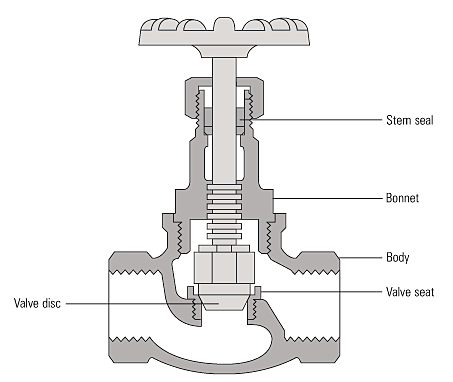 |
Fig. 12.1.2 A conventional globe valve
|
Globe valves are less likely to leak than gate valves,
which means that they can be used for higher pressure or higher volume
applications, for example in steam systems, or where fluid loss can be
hazardous or costly. The increased cost of globe valves over gate
valves is therefore offset by the additional safety they provide, and
a reduced chance of fluid loss.
The pressure of the fluid acting over the area of the
disc generates an axial load on the stem. This makes closing the valve
difficult, so much so, that it limits the size of a standard globe
valve to DN250. On high differential pressure closed systems,
balancing plugs can be used to overcome this effect, allowing valves
with a nominal diameter of up to 500 mm to be used (Figure 12.1.3(a)).
The balancing plug contains a pre-lifting plug that acts as a pilot
valve. When the valve is opened, the pre-lifting plug opens first,
allowing the medium to pass through it at a controlled rate
(Figure 12.1.3(b)). This reduces the differential pressure across the
valve, enabling the disc to be easily lifted off its seat (Figure
12.1.3(c)). To assist closing of the valve, isolation valves fitted
with a balancing plug have to be fitted in reverse so that the top of
the plug is acted on by the upstream pressure.
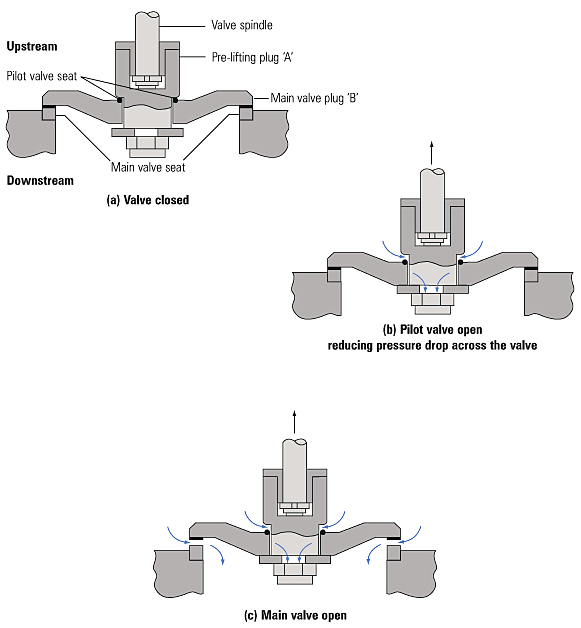 |
Fig. 12.1.3 Schematic of a typical balancing
plug valve
------------------------------------------------------------------------------------------------------------------------
|
|
Hydraulic actuator |
A device fitted to the valve stem than uses
hydraulic energy to open and close the valve. Depending on the
configuration, the hydraulic fluid may both open and close the
valve, or just open the valve. In that latter case, a spring will
typically be fitted inside the actuator to return it (and the
valve) to the closed position.
------------------------------------------------------------------------------------------------------------------------ |
Jacketed valve |
This valve is design incorporates a so-called jacket
around the valve body. Steam is introduced into the jacket to keep
the fluids being controlled at the required temperature.
------------------------------------------------------------------------------------------------------------------------ |
Lift check |
This non-return valve design incorporates a piston
to damp the disk during operation.
------------------------------------------------------------------------------------------------------------------------ |
Line blind |
A pipeline shut-off device, whereby a flat disk is
forced between two flanges. Line blinds are less expensive than
valves, but require much more time to operate.
------------------------------------------------------------------------------------------------------------------------ |
Linear valve |
See multi-turn
------------------------------------------------------------------------------------------------------------------------ |
Multi-ported |
Multi-ported valves include additional inlet/outlet
ports, to allow fluids to be directed. The ball and plug valve
types are ideally suited to multi-port designs.
------------------------------------------------------------------------------------------------------------------------
|
Multi-turn |
Category of valves (such as gate, globe, needle)
which require multiple turns of the stem to move the valve from
the fully open to the fully closed position. Also known as linear
valves. See also quarter-turn.
------------------------------------------------------------------------------------------------------------------------ |
Needle valve |
This multi-turn valve derives its name from the
needle-shaped closing element. The design resembles that of the
globe valve. Typically available in smaller sizes, they are often
used on secondary systems for on/off applications, sampling, etc.
------------------------------------------------------------------------------------------------------------------------ |
Penstock valve |
A type of simple gate valve, used to contain fluids
in open channels. Often found in waste water treatment plants.
------------------------------------------------------------------------------------------------------------------------ |
pH
PH is a term that refers to the relative concentration of hydrogen
ions (H+) in a solution,
and therefore whether the solution is acid
or base.
It's a lot easier to refer to the pH of a solution than to
the "negative logarithm of the hydrogen ion concentration!"
Acids have pH values of seven or below: Bases have pH
values of seven or higher. If you lower the pH of
a solution, then you are making it more acidic. If you raise
the pH of a solution, you are making it more basic.
------------------------------------------------------------------------------------------------------------------------ |
Pilot valve |
Small valve requiring little power which is used to
operate a larger valve. See also solenoid valves.
------------------------------------------------------------------------------------------------------------------------ |
Pinch valve |
A valve in which a flexible hose is pinched between
one or two moving external elements to stop the flow. This valve
is often used in slurry and mining applications, as its operation
is not affected by solid matter in the medium. It is also used
with certain gases, as the absence of possible leak paths to the
atmosphere ensures good emission control.
------------------------------------------------------------------------------------------------------------------------
Piston valves
One of the main disadvantages of linear movement valves is the fact
that their seats are prone to damage from dirt and wiredrawing, and
therefore, depending on the application may require regular
maintenance. Although these seats are replaceable in theory, it
usually involves significant time and cost, and it is often more
advantageous to replace the entire valve. To overcome this problem,
piston valves have been developed.
The piston valve is a variant of the conventional globe valve, with
the traditional seat and cone replaced by a piston and lantern bush.
The piston is connected to the valve stem and handwheel, and passes
through two sealing rings that are separated by a lantern bush. When
assembled, the two sets of sealing rings are compressed around the
piston by the load exerted along the stem. The upper set of sealing
rings acts as conventional gland packing, and the lower set acts as
the seat. Furthermore, the large sealing area between the piston and
rings assures a high level of shut-off tightness.
The piston valve is not designed for throttling duties and must be
used in the fully open or closed positions. When the valve is fully
opened, only the bottom face of the piston is exposed to the fluid as
the rest of the body is protected by the upper sealing rings. This
means that the sealing surfaces (the sides of the piston) are
protected from erosion by the fluid flow.
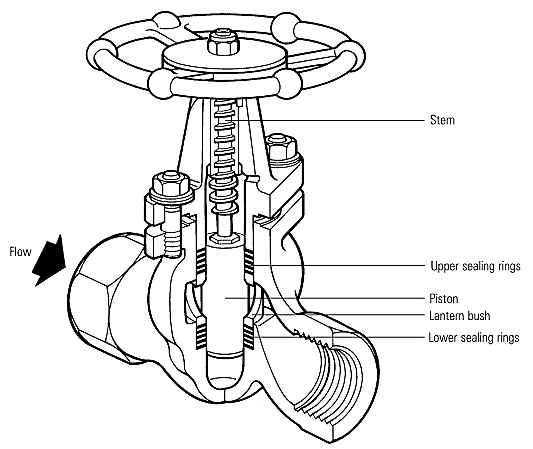 |
A piston valve
|
If the valve requires maintenance, all the internals
can be easily removed by undoing the cover nuts and withdrawing the
piston. The rings and the lantern bush can then be removed using an
extractor tool. This operation is simple and can be undertaken without
having to remove the valve from the pipeline. In general, the piston
should never have to be replaced, but the sealing rings may wear over
a long period with frequent operation.
------------------------------------------------------------------------------------------------------------------------
|
Plug valve |
This multi-turn valve derives its name from the
rotating plug which forms the closing element. The plug may be
cylindrical or truncated. In the open position, the fluid flows
through a hole in the plug. Lubricated plug valves rely on a
sealing compound injected between the plug and the valve body,
whilst sleeved plug valves are fitted with a ‘soft’ insert
between the plug and the body.
------------------------------------------------------------------------------------------------------------------------ |
Pneumatic actuator |
A device fitted to the valve stem than uses
pneumatic energy to open/close or regulate the valve. Depending on
the configuration, the compressed air may both open and close the
valve, or just open the valve. In that latter case, a spring will
typically be fitted inside the actuator to return the valve to the
closed position.
------------------------------------------------------------------------------------------------------------------------ |
Positioner |
Device that ensures the closing or throttling
element of a valve moves to or maintains the correct position.
------------------------------------------------------------------------------------------------------------------------ |
Pressure reducing valve |
A self-operating valve used to reduce any excess
pressure in a system, eg steam. Also known as a PRV. The valve
opens if the internal pressure exceeds that holding the closing
element onto the seat.
------------------------------------------------------------------------------------------------------------------------ |
Quarter-turn |
Category of valves (such as ball, plug, butterfly)
which require just a 90 degree turn of the stem to move from the
fully open to the fully closed position. See also multi-turn.
Note: some larger valves may, for simpler manual operation, be
fitted with gearboxes, giving them the appearance of a multi-turn
valve.
------------------------------------------------------------------------------------------------------------------------
Rising/non-rising stems - If the stem is rising, it will
move vertically upwards when the valve is opened, as opposed to only rotating, as with a non-rising
stem. The rising stem indicates the degreee of valve opening,
which in turn roughly reflects the amount of flow through the
valve. Valves with rising stems do however require more space
above the bonnet to accommodate the stem in the fully open
position. The use of non-rising stems is recommended on gland
packed valves, as they reduce the wear on the packing.
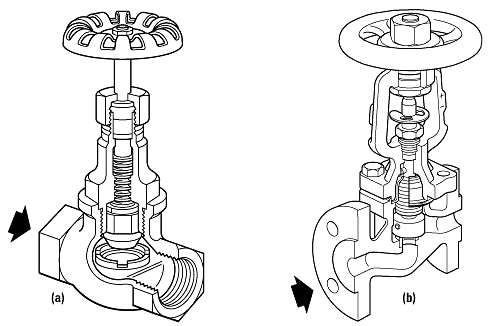 |
Rising (a) and non-rising (b)
stem valves
|
------------------------------------------------------------------------------------------------------------------------
|
|
Reduced bore |
Indicates that the internal diameter of the valve is
lower than the piping to which the valve is fitted.
------------------------------------------------------------------------------------------------------------------------ |
Regulating valve |
This valve type is used to regulate flows to provide
a constant pressure output.
------------------------------------------------------------------------------------------------------------------------ |
Sampling valve |
A valve which is fitted to a reactor or pipeline to
allow small sample of a fluid to be withdrawn for further testing.
In simple cases a standard gate or needle valve, for example, may
be used. The disadvantage is, that inappropriate use may result in
spillage. As an alternative, valves are available which ‘trap’
a small quantity of fluid in a chamber, and only this small amount
of fluid is released when the valve is operated.
------------------------------------------------------------------------------------------------------------------------ |
Solenoid valve |
Solenoid valves, typically of the needle globe type,
are operated by an electrical solenoid. They are often deployed as
pilot valves, i.e., fitted to actuators which in turn control
larger valves.
------------------------------------------------------------------------------------------------------------------------ |
Spring return |
See Pneumatic actuator.
------------------------------------------------------------------------------------------------------------------------ |
STRUM BOX
A perforated metal box fitted around a
bilge suction pipe opening to prevent debris from choking the pipe
and bilge pump |
------------------------------------------------------------------------------------------------------------------------ |
Subsea valve |
A valve which is designed for use in sea water. For
example, installed in a pipeline on the sea bed.
------------------------------------------------------------------------------------------------------------------------ |
Swing check |
This non-return valve has a hinged disk as the
closing element.
------------------------------------------------------------------------------------------------------------------------ |
Tank valve |
A valve arranged for fitting at the bottom of a tank
or process vessel.
------------------------------------------------------------------------------------------------------------------------ |
Wafer design |
The construction of wafer design valves allows them
to be ‘sandwiched’ between flanged sections of pipeline. The
benefit is lower bolting requirements. Typically used with certain
butterfly and check valves.
------------------------------------------------------------------------------------------------------------------------ |
Wellhead valve |
Wellhead valves are used to isolate the flow of oil
or gas at the takeoff from an oil or gas well. The design is
usually a plug or gate valve.
------------------------------------------------------------------------------------------------------------------------ |
WOG
WOG - A pressure rating in psi for valves. W. Water, O. Oil, G.
Gas(04011) |